Topics Covered
Summary
Understanding helmet certifications like DOT, ECE, and Snell is crucial for rider safety. These standards test helmets for impact resistance, penetration protection, chin strap strength, and vision clarity. While DOT is the U.S. minimum legal requirement, ECE (used in Europe) and Snell (a voluntary, high-performance standard) offer stricter safety measures. Each certification has different testing methods, with ECE 22.06 incorporating the latest research. Choosing the right helmet ensures maximum protection in real-world accidents.
WHAT’S THE DIFFERENCE BETWEEN SNELL, DOT, ETC.
Ever wondered what those labels on your helmet really mean? What do they stand for, and which one should you trust? These are the questions that pop into every rider’s mind when they’re about to buy a helmet.
Whenever you buy a helmet, whether it’s online or in a store, you’ll notice labels like DOT, ECE, or Snell. These certifications all have one main job: keeping your head safe in a crash. They test helmets in similar ways a head-shaped form is put inside the helmet and dropped from different heights onto various surfaces at different speeds. There’s also a penetration test, where a sharp object is dropped on the helmet to see if it holds up. Finally, they test how strong the chin strap is. Keep in mind, though, that even though the tests are similar, the standards for each certification are different. This is especially important when choosing touring motorcycle helmets, as long rides require both comfort and top-tier protection.
According to the National Highway Traffic Safety Administration (NHTSA), wearing the right motorcycle helmet can mean the difference between life and death.
Note: This info comes from careful research and talking to experts. It’s not a promotional post we’re just here to help riders make smart choices.
DOT FMVSS 218:
Motorcycle helmets are a lifesaver, literally. To keep riders safe, the U.S. Department of Transportation (DOT) makes sure that every helmet sold in the U.S. meets certain safety standards, known as FMVSS No. 218. This standard sets the baseline for what a helmet needs to do to protect your head in a crash. The DOT tests different helmets every year to make sure they’re up to par.
Because helmets are so crucial for keeping riders safe, many states have laws that require helmets to meet these safety standards, all helmets sold in the United States must have a DOT FMVSS 218 label but some riders still choose to wear helmets that don’t make the cut, often going for novelty helmets that aren’t actually safe.
DOT FMVSS 218 refers to the Department of Transportation’s Federal Motor Vehicle Safety Standard No. 218. This is a set of regulations in the United States that establishes the minimum safety requirements for motorcycle helmets. There are myths about DOT that they never updated their tests when they were established but actually, they evolved lastly, they updated in 2013 probably, so you can trust DOT certificates as well. They mainly perform four major tests (Crash test, penetration test, chin strap test, and Vision test) under different weather conditions. So, if a helmet passes all these tests then it is safe to sell in the market or if the helmet fails in the test, it is considered illegal to sell and use this type of helmet.
Crash Test/Impact Attenuation
Test procedure
- Helmet Placement: The helmet is placed on the head form, ensuring it fits securely and is positioned correctly.
- Drop Test: The helmet is tested by dropping a flat and hemispherical impactor, which is a heavy, solid object, from a maximum height of 1.8 meters (about 5.9 feet). The impactor weighs around 5 kg (about 11 pounds). Sensors placed inside the helmet and headform measure the force of the impact. If the force exceeds 400 Gs, the helmet fails the test.
- Impact Locations: Helmets are tested at multiple locations on the helmet shell to simulate different types of impacts that might occur in real-world scenarios. Common test points include the top, sides, and front of the helmet.
Penetration Resistance:
The goal of the penetration test is to evaluate the helmet’s ability to resist penetration by a sharp object. This is important because penetration can lead to severe head injuries if a sharp object punctures the helmet and makes contact with the rider’s head.
Test Procedure:
- Helmet Placement: The helmet is snugly fitted onto a test head, just like how you’d wear it, to make sure it’s positioned correctly.
- Drop Test: A sharp, pointed object is dropped from about 4 feet onto the helmet. This tests if the helmet can handle impacts from sharp debris without letting the object penetrate through.
- Penetration Locations: The helmet is hit at different spots—like the top and sides—to see if it can stop the pointed object from piercing more than 10 mm or reaching the test head inside.
Effectiveness of The Retention System
The retention system, or chin strap, ensures the helmet remains securely on the rider’s head during impacts, preventing roll-off and maximizing protection against head injuries.
Testing Procedure:
Helmets are fitted snugly on a test headform, then subjected to a tension load of 23 kg for one minute, followed by a heavier load of 38 kg to assess the strength and prevent excessive movement (no more than 30 mm deflection).
Importance: A reliable retention system enhances impact protection, ensures compliance with safety standards, and boosts rider confidence by keeping the helmet in place during a crash.
Vision Test:
Checking the Field of Vision: DOT ensures that helmets provide a clear view. This means the helmet should allow you to see well to the sides, up, and down—just like you would without the helmet on.
Testing Procedure:
The helmet is placed on a test head form, and measurements are taken to check how much of your peripheral vision (side view) is covered. The goal is to make sure the helmet doesn’t block your view and lets you see a wide area.
- Standards for Passing: For a helmet to pass DOT’s vision test, it must offer a horizontal field of vision of at least 105 degrees and a vertical field of vision of 28 degrees. If the helmet restricts your vision more than these limits, it fails the test, which means it might limit your ability to see clearly while riding.
DOT relies on independent companies to handle all helmet testing. Surprisingly, many helmets sold with a DOT certification sticker still fail safety tests, yet they remain on store shelves. This happens because DOT doesn’t conduct its own tests but instead relies on outside companies to do the job. To keep manufacturers in check, DOT imposes hefty fines and other penalties, hoping this will push them to produce safer helmets.
Riders have a real challenge when it comes to helmet safety. Sure, you need a DOT-approved helmet to be legal in many states, but that doesn’t always mean the helmet meets the tougher FMVSS 218 standards. This is why having extra safety certifications is so important—they give you peace of mind, knowing your helmet will actually protect you when you need it most.
ECE 22.05 and 22.06
ECE (Economic Commission for Europe) actually sets the rules and regulations for many industries including transportation. In simple words if you want to ride even a simple Cruiser Motorcycle, You need a Helmet that have a label by ECE to ride on public roads in Europe.
The ECE 22.05 standard was introduced in 2000, while the latest version, ECE 22.06, came out in 2020. While different organizations have their own testing standards, their shared goal remains the same: ensuring helmets provide a minimum level of protection to reduce serious injuries in the event of an accident. Some organizations may apply more rigorous testing, but this is the key distinction between them. Similarly, the main difference between ECE 22.05 and ECE 22.06 is the testing approach—ECE 22.06 uses more advanced methods based on the latest research to thoroughly evaluate helmet safety.
Lets have a detail discussion on testing system so you can make a better choice of your helmet for any type of ride.
Impact Attenuation Test:
This test is conducted by a impactor machine which have a steel impactor or anvil and a representive helmet is droped onto anvil at both low and high speed and a sensor is placed inside the helmet with headform. Helmet is tested with all the extra systems like visors and communication systems.
Procedure:
Impact Locations and Types:
Test Locations: The helmet is subjected to impacts at multiple locations on the helmet shell. These locations typically include:
- Front: Around the forehead area.
- Side: Near the temple region.
- Rear: At the back of the helmet.
- Top: On the crown of the helmet.
- Impact Types: Helmets are tested for:
- Direct Impacts: Where the helmet strikes the impactor directly.
- Oblique Impacts (Angular Impacts): Where the helmet strikes the impactor at an angle, simulating rotational forces.
Impact Absorption Test Procedure
Drop Tests:
- Standard Velocity: The helmet is dropped from 2.87m height onto the rigid flat and Kerb anvil at a speed of 7.3ms.
- High Velocity: The helmet is dropped from 3.43m height onto the rigid flat anvil at speed 8.3ms.
- Low Velocity: The helmet is dropped from 1.84 height onto the rigid flat and Kerb anvil at speed 6.0ms.
- Oblique Impact: The helmet is dropped from 3.43 height onto the rigid flat and 45degree oblique anvil at 8.0ms.
For oblique impacts, the helmet is struck at an angle to simulate rotational forces.
Measurement:
- Accelerometers inside the helmet measure the force of the impact and how much energy is absorbed by the helmet.
- The helmet’s ability to dissipate energy and reduce the amount of force transmitted to the headform is assessed.
- Helmet is then sent for the detail checking the points of damage and all other stuff like this.
The ECE 22.06 impact absorption test aims to ensure that helmets provide effective protection against both direct and angular impacts. This standard represents a significant improvement over previous standards by incorporating rotational impact testing to address the complex nature of real-world motorcycle accidents.
Penetration Test:
The ECE Penetration Test is a vital part of the helmet certification process. It checks whether helmets can withstand sharp or pointed objects, ensuring they don’t penetrate and harm the rider’s head. This test is included in both the ECE 22.05 and the updated ECE 22.06 standards, with the latter having stricter requirements. By meeting these standards, helmets can provide better protection against potential dangers, making them safer for riders on the road.
Test Procedure:
- Getting Set Up: The helmet is placed on a head-shaped dummy, making sure it stays still during testing for accurate results.
- Using the Right Tool: A pointed metal object, weighing about 3 kg (6.6 lbs), is used for testing. It has a conical or pyramid shape, mimicking sharp items that could cause harm in a crash.
- Dropping the Object: The pointed object is dropped from about 3 meters (10 feet) onto different parts of the helmet. This simulates a sharp object hitting at high speed.
- Testing Locations: The drop happens on various spots, including the crown, front, sides, and back, plus vulnerable areas like vents or protrusions.
Testing Criteria:
The main goal is that the pointed object should never break through the helmet’s outer shell or inner padding. If it reaches the dummy’s head, that’s a fail. Some bending of the helmet’s outer layer is okay, but it should never allow the sharp object to touch the dummy’s head.
CHIN Strap Test:
This test is crucial because it makes sure that the helmet will stay on the rider’s head during an accident. If the helmet comes off, it can’t protect the rider, so a reliable retention system is vital.
Procedure
First, the helmet is placed on a headform, ensuring it fits snugly.
- Applying Weight: A hefty weight, usually around 50 kg, is attached to the chin strap. The weight is hung from the strap for about 30 seconds, giving it time to really test the helmet’s retention capabilities.
- Observation and Inspection: While the weight is hanging, testers closely watch the helmet for any signs of failure, such as the chin strap tearing or the helmet slipping off. After the weight is removed, they conduct a thorough inspection to check for any damage.
Testing Criteria
- Staying Secure: For the helmet to pass the test, it must stay securely in place on the headform without slipping or detaching at all.
- Strap Durability: The chin strap should remain intact and not show any signs of tearing or excessive stretching throughout the test.
- Strong Attachment Points: The points where the chin strap connects to the helmet need to be robust, showing no signs of deformation or damage.
3 more tests perform to check the performance of Shell, visor and other accessories behave in case of accident. All these tests performed under different temperatures and humidity
Vision Test And Other Accessories:
- Purpose: To check how well the visor provide vision, how much rider can see the surrounding and what is the performance of Other Accessories, in case of accident, how they behave
- Criteria: The helmet should provide a clear, unobstructed view while offering full protection from debris and other potential hazards, also pose a minimal effect in case of impact
Shell Test:
Once all the tough tests are done, the inspection team carefully checks the helmet again, especially focusing on the outer shell. The shell shouldn’t bend or change shape too much because it’s designed to stay strong during impacts. If it deforms too much, it means the helmet might not protect you properly in an accident. The shell has to stay tough and meet safety standards to keep you safe.
Testing Criteria of Snell
You’ve probably heard the story behind SNELL on social media—it’s pretty well-known. The testing process is similar to what we’ve talked about before, but the key thing that makes SNELL stand out is that they operate independently. Manufacturers actually send their helmets to SNELL for testing, instead of self-certifying like some other standards (looking at you, DOT!). So, if a helmet gets SNELL certified, it’s because it passed some pretty tough, independent tests.
Testing details are discussed here:
Impact Test:
A helmet is placed on metal headform and dropped on steel anvil of flat, hemisphere, roll bar, kurbstone, edge or a horseshoe, in a valid test the force on sensor does not exceeds 260-300 G’s according to SNELLS and other experts, otherwise the helmet will be rejected.
Positional Stability Test:
This test is a crucial test for a helmet to check if the helmet stays on the head in case of an accident.
They place a head form at a 135-degree angle and fit the helmet on it. A rope is hooked to the back of the helmet and a 4 kg weight is dropped, pulling on the helmet to test how well it stays on. The helmet can move but shouldn’t come off. Then, they rotate the head form, hook the rope to the front, and do the same test. Again, the helmet can shift but must not fall off.
Chin Strap & Chin Bar Test:
The helmet’s chin strap is tested to make sure it can handle real-life impacts without breaking. They attach a weight of about 23 kg to the strap and see if it holds up under the pressure. If the strap can’t support the weight, it fails the test. For full-face helmets, they go a step further by testing the chin bar (the part covering the chin). In this test, a 5 kg weight is dropped onto the center of the chin bar, and the goal is to measure how much it bends. If the bend goes beyond the safe limit, it doesn’t pass. These tests help ensure that the helmet can provide strong protection where it matters most.
Penetration Test:
A 3kg pointed object is dropped on a helmet to check if it penetrates, or even touches the head form, in both cases helmet fails in the penetration test.
Face shield Test:
The face shield penetration test checks if the visor on full-face motorcycle, racing, and karting helmets is tough enough to protect your face. They attach the visor to the helmet and shoot it in three different spots using an air rifle. The pellet travels super fast, around 500 km/h.
For all types of helmets, the pellet shouldn’t go through the visor. For racing helmets, there’s an extra rule: any bump on the inside of the visor caused by the impact shouldn’t stick out more than 2.5 mm. This makes sure the visor can handle flying objects without putting the rider at risk.
Chin-Bar test:
The chin bar impact test checks if the chin area of racing helmets can protect during a crash. In the test, they place the helmet on a holder that drops straight down onto a flat surface, hitting the chin area.
Inside the helmet, there are sensors to measure the shock felt by the “head” inside. For the helmet to pass, it needs to hit the surface at a speed of at least 5.5 meters per second, and the force on the head inside shouldn’t be more than 275 G. If it meets these requirements, the helmet is considered safe for protecting the chin in an impact.
Two more tests also performed for the special racing helmets: Flame Test & Frontal Head Restrain Test.
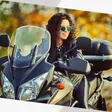
As the CEO of Wheel Twist and a passionate long rider, I personally test motorcycle gear to ensure it meets the needs of fellow travelers. My content reflects my love for adventure and commitment to the riding community.